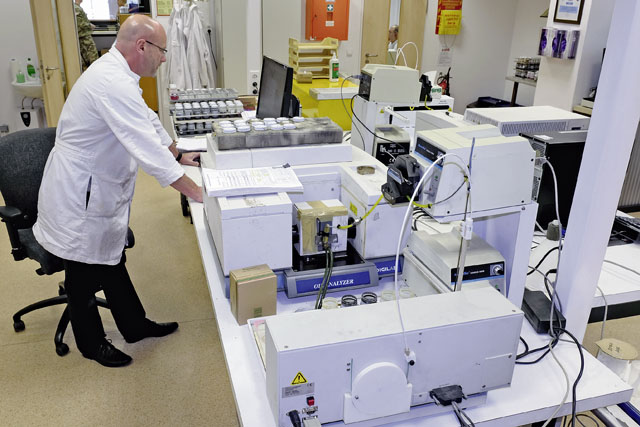
The Army Oil Analysis Program lab on Kleber Kaserne works every day to increase readiness and lower maintenance costs while also helping to protect the environment.
AOAP is part of a Department of Defense-wide effort to predict equipment component failures and lubricant conditions by testing oil samples from vehicles, generators, aircraft and other kinds of equipment. The program’s goal is to improve combat readiness and reduce equipment failures while conserving resources by reducing the frequency of unnecessary oil changes.
“Right now, we do about 1,000 samples a month,” said Heidi Bodeit, the Kaiserslautern AOAP lab’s director.
Units enrolled in the program submit oil samples which are tested on a regular basis. By examining the contents of the oil, the laboratory personnel can determine if the oil is going bad or the equipment needs maintenance.
“We are the oil doctors,” said Dr. Davoud Tehranfar, who holds a doctorate in chemistry.
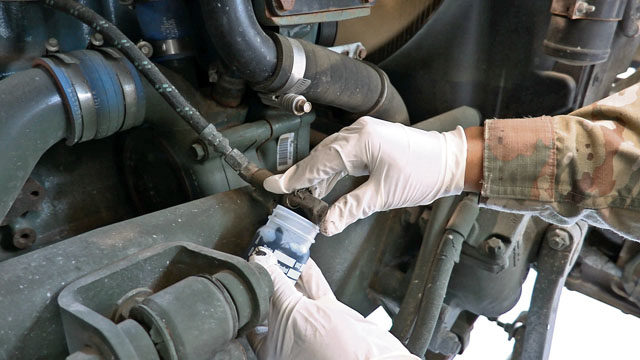
The lab measures how healthy the oil is, he said. He compared it to doing laboratory tests on a person’s blood sample.
Testing starts with an examination of the oil’s viscosity, or thickness. This helps tell if the oil is still “healthy” for use or needs to be replaced.
Mileage or time may indicate a vehicle needs an oil change, but the oil may still be working as it should, Bodeit said. Getting rid of oil unnecessarily costs the American taxpayer money, she said.
Other tests look for particulates like water, metals or fuel, which may get into the oil if the equipment is not running properly.
When looking for particulates, there are three tests for ground vehicles and 4-6 tests for aircraft, Tehranfar said. Detlef Nuss, a physical science technician who performs many of the tests, has worked at the lab for 35 years. One of the tests he performs uses an atomic emission spectrometer to determine what elements are in the oil.
By examining the degree to which 15 elements are present in the oil, the lab can determine what may be ahead for the vehicle. For example, too much iron may indicate a problem in the engine case, Tehranfar said.
“The oil is talking and we have to find the language,” he said.
They also track oil samples from a vehicle, keeping a record of each successive sample, he said. If subsequent tests showed a vehicle’s engine condition getting worse, they can notify the unit to take a look at what may be wrong.
The Kaiserslautern AOAP lab serves all the units in Europe and Africa, Bodeit said.
“We have a very close and good relationship with the EUCOM deputy G-4,” she said.
The lab also supports the equipment in the Army Prepositioned Stocks around Europe and the equipment in the Baltic states for the new rotational forces, she added.
The 39th Transportation Battalion has a fleet of 60 vehicles that are sampled every month, said Chief Warrant Officer 2 Cherenfant Pierrelouis, the maintenance supervisor.
The program saves the unit about $28,000 a quarter in oil purchases alone, he said.
There are additional savings in parts, such as oil filters, and man hours not used unnecessarily, Pierrelouis said.
It takes one mechanic about 45 minutes to change oil and dispose of it, however one mechanic can draw samples of both engine and transmission oils in five to ten minutes, he added.
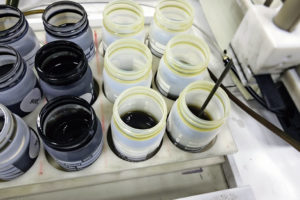
After pulling the samples from equipment, units can send the bottles through the mail or by delivery service to the lab.
The lab has 72 hours to analyze samples from ground equipment and send results back, Bodeit said. For aviation samples, the response must be within 24 hours.
If there is nothing wrong with the oil, the response will be an email. If something is wrong, the lab workers will call the unit directly, she added.
In this way, AOAP increases unit readiness by letting commanders know which vehicles have problems before they show up during a mission, Bodeit said.
The Kaiserslautern lab only takes oil from vehicles that are required to be enrolled in AOAP, but Bodeit hopes to expand the program, encouraging commanders to voluntarily enroll.
Another benefit of AOAP is the reduction in waste oil and other items, like oil filters, that accumulate after unneeded oil changes.
“AOAP is a good program, not only for the readiness and the safety, but also for the environment,” Bodeit said.
To serve customers better, the lab undergoes a yearly ISO 9000 certification by the International Organization for Standardization. In fact, the AOAP lab in Kaiserslautern is the only Army Oil Lab in the world certified as ISO 9000 compliant.
ISO provides a set of international standards on quality management and quality assurance developed to help companies maintain an efficient quality system.
The certification demonstrates the customer gets a good quality product or service, Bodeit said.
The lab, which employs five people, is getting ready to update its certification this year under the latest standard, ISO 9001:2015.
It takes a lot of work and documentation to become ISO 9001 compliant, said Akwasi Opoku Edusei, who has been working on the certification.
“It’s not easy to get,” he said.