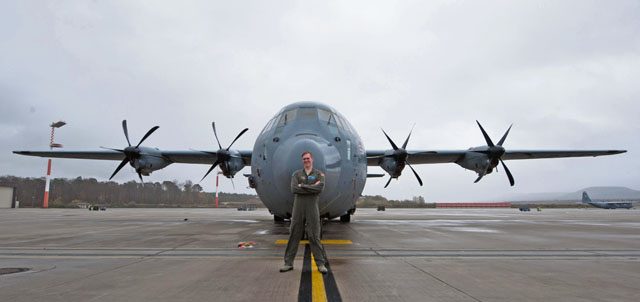
Team Ramstein is embracing its culture of innovation by putting a new way to inspect its units and Airmen into action.
Continuous Process Improvement is a program focused on driving performance improvement and cost reduction through data-driven decisions. Processes are constantly evaluated and improved in light of their efficiency and effectiveness. Feedback from the process and customer are evaluated against each other and the organization’s goals.
Lydia Bradley, 86th Force Support Squadron management analyst, believes Airmen are the front line of innovation.
“Airmen are at the tactical level, performing the processes, and therefore they witness the problems and issues,” Bradley said. “The application of CPI principles enables Airmen to integrate continuous improvement into day-to-day operations across the full spectrum of AF operations.”
The goal of Air Force CPI is to eliminate waste while maximizing customer value. It uses several process-improvement methodologies, including lean, six sigma, theory of constraints and business process reengineering. Key principles contained in these methodologies include improving flow and reducing waste within a process, focusing on factors that degrade product quality, identifying and overcoming process constraints and redesigning processes.
“Continuous process improvement is a hallmark of highly successful organizations,” Bradley said. “Wasteful, ineffective or unsafe ways of doing business cannot be tolerated. Commanders must foster a culture of innovation and challenge inefficiencies.”
The program aligns its goals with Air Force Instruction 90-201, The Air Force Inspection System, which states, “Units should show a fostered culture of innovation and its members should be encouraged to challenge inefficiencies. A process for identifying and fixing deficiencies should be established and followed.”
Some Airmen that exemplify this are Staff Sgt. James Gaston and Airman 1st Class Patrick Stone, 37th Airlift Squadron loadmasters. Gaston implemented a repair program that salvages usable parts from nonfunctional headsets to create complete units. Leveraging his background as a mechanic, Gaston identified the broken components in the headsets and developed a process to repair or replace the broken parts.
He then spent the time to train Stone to perform headset repairs, making the repairs a continuous, transferable process improvement. In the first iteration of their program, Gaston and Stone were able to assemble nine fully functional headsets from individual components, thus reducing the number of new headsets purchased. Together, they saved the Air Force $8,100.
It’s something Stone believes is inside his unit’s culture.
“We always want to get the job done, and as we discover more efficient methods to do so, it proves how much we strive for excellence,” Stone said. “It may be a matter of doing something slightly different or implementing an entire new system. Regardless, we’re devoted to innovation.”
In order to continue enabling theater and strategic airpower, Ramstein has to maintain integrity in its work force. CPI is intended to help Airmen embrace their culture of innovation by shedding waste, finding more effective ways to accomplish the mission and providing Airmen more ability to help the unit find shortcomings and strengthen key assets.